Economical, Accurate Gantry Table Key to Development of New Laser Scanner Line

Time to Read: 4m 0s
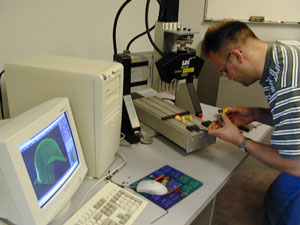
Laser Design grew out of Schuster’s recognition that the need of many companies for highly accurate coordinate data on their manufactured products was going unmet. Schuster gathered a team talented group of engineers and software developers and developed line-sensor technology dramatically reduces scanning time by collecting data substantially faster than conventional measuring technologies. The company's technology uses laser triangulation, an active stereoscopic technique where the distance of the object is computed by means of a directional light source and a video camera. The scanner emits a Class II laser light, which scans an object. The scanning systems use a line range profiling that spreads the laser beam into a line and collects data up to 100 times faster than point range sensors and up to 15,000 coordinates per second. Using triangulation-based technologies, 3D coordinate locations lying on the surface of the object are captured by a sensor on a charge coupled device in the probe according to scan density and pattern parameters set by the user. Details of the object’s shape and finish are captured with high accuracy.
Duplicating complex shapes
High density, true surface information permits exact duplication of complex shapes. Digitizing eliminates the inaccuracies of mechanical probe offsets, deflection, vector analysis, and probe size or shape. Laser scanning non-contact technology also allows difficult materials such as clay, fabric, wood, foam, plaster, glass, metal, and plastic to be scanned without damage to the surface of the object. A laser beam is projected from the sensor head onto a scanning object. The object scatters the light, which is then collected by a video camera located at a known triangulation distance from the laser. Using trigonometry, the 3D spatial (XYZ) coordinates of a surface point are calculated. The charge coupled device camera’s 2D array captures the surface profile’s image and digitizes all data points along the laser. With specialized inspection software from solution partners, the laser scan data can be easily compared to a CAD file enabling deviations from nominal to be graphically displayed. Other software programs allow NURBS surfaces to be applied to the scan data to create a CAD Model of the scanned object. STL and CNC toolpaths can be derived from the scan data for duplication and manufacturing.Laser Design's Surveyor 3D laser digitizing systems are used for rapid inspection applications, including computer-aided verification and quality control, reverse engineering, rapid prototyping, and manufacturing. Typical parts scanned include plastic and rubber components, EDM electrodes, extrusions, mold, dies, and castings. Laser Design systems' scanning speed and accuracy are ideal for quality inspection. Scan data from actual parts can be compared to 3D CAD models with graphic software like Geomagic Qualify, PolyWorks Inspector and others. By scanning an existing product or tool, editing, and outputting the scan data to a CAD system, improved product designs can be completed very quickly, reducing the design cycle time. Models that have been produced by a sculptor or rapid prototyping system are scanned for input into CAD. Surfaces can be applied to the scan data using software such as Raindrop Geomagic. CNC toolpaths can be generated direct from 3D scan data files using optional software. This accelerates mold/tool/die production and the CNC carving process immensely. Core and cavity toolpaths for a variety of cutters can be produced from a single set of scan data.
Need for a lower cost alternative
About a year ago, through conversations with customers Schuster identified the need for a lower cost alternative-scanning tool for reverse engineering. At this point, all of the company’s products were priced at above $100,000. "All of our machines available at that time used servo controls," Schuster said. "Other machines were available at a lower price but they all used manual motion to control the scanning heard. The problem with this approach is that manual motion introduces jerkiness and instability that reduces the accuracy of the resulting 3D model. What we really needed was a motion control system that would provide us with the accuracy of servo control at an economical cost. Then we discovered the Techno gantry from Techno, Inc., New Hyde Park, New York which offers travel ranging from 8 by 10 by 5 inches up to 56 by 96 by 20 inches. This mechanical system delivers durable, play-free motion that is rigid and stable. Yet the cost was low enough that we were able to introduce a new line of machines that each cost about 50% less than existing machines of comparable size." Schuster was pleasantly surprised to find that Techno not only sold the machines for CNC applications but also made them available for other OEM applications such as scanning and inspection.Each Techno gantry base incorporates THK linear motion system for high load-carrying capacity, rigidity and positioning accuracy. Heavy cast aluminum side plates support the X axis and provide increased stiffness. All axes include a home reference switch and a far end limit switch with +0.01mm. repeatability. THK profile rail and bearing block systems produce very smooth, play-free motion, thus facilitating high accuracy cuts or scans. Another feature of the machine that Schuster found appealing was its use of anti-backlash ball screws, like those used in high-end machining centers. These screws have excellent power transmission due to the rolling ball contract between the nut and screws and also feature extremely small backlash. Rolling ball contract between the nut and screw provides excellent rigidity and ensures long life because wear is considerably lower than ACME screws and nuts which have sliding friction contact. This type of contact ensures low friction, low wear, and long life. The ball screws also contribute to the bases exceptionally high positioning accuracy per axis of 0.004 inches/ft, resolution of 0.0004 inch and repeatability per axis of 0.0004 inch.
Schuster said that once he had selected the Techno gantry base it only took about one week to complete the design of the new laser scanner. The design process primarily consisted of integrating the company’s existing scanner head and software with the gantry base. The result is the RE series of 3D laser digitizers, which scan parts from all orientations and then easily rotate the data back into a common coordinate system. Laser Design’s Surveyor Scan Control software controls scanning motion and sensor settings and contains advanced data-editing and automation features. The digitized scan data can be processed further with optional software from Laser Design’s partners. The new laser scanners have already established a large base of customers in a wide range of different industries. For example, one of the world’s largest theme parks uses the new scanners to generate 3D CAD models from concept models. In a typical application, they might scan a 3 foot high model of a cartoon characterize and use the resulting CAD model to manufacture a 60 Foot high version with CNC machine tools. "The customer reports that they can produce the finished product in between 1/20 and 1/10 of the time that used to be required when they were creating CAD models by hand," Schuster said.
For more information contact: Techno, Inc. Linear Motion Systems, 2101 Jericho Turnpike, New Hyde Park, NY 11040. Phone: 516-328-3970 Fax: 516-358-2576 E-mail: TECHNO LINEAR MOTION SYSTEMS.